Főoldal » Műszaki fejlesztés » Egyéb fejlesztések
Egyéb fejlesztések
A DR-PAck diagnózisa: Az extruder pollen allergiás
A DR-PAck Kft. elsősorban fújt fólia gyártásával és ezzel kapcsolatos technológia fejlesztésével foglalkozik, ezen írásunkban bemutatandó probléma érinti a fóliagyártás, sőt a műanyaggyártás szinte valamennyi területét. Diagnózisunk mindenképpen túlmutat a fóliagyártásnak ezen „szűk" területén, így széles érdeklődésre tarthat számot.
A sok receptúrával dolgozó gyártó rendszerek granulátum ellátása a következőképpen épül fel. Az extruder egy granulátum felszívó-adagoló-keverő egységgel van ellátva, melynek feladata az adott receptúrának megfelelő granulátum keverék folyamatos biztosítása a gép számára. A felszívó egység a garnulátumot a tárolóból felszívja, majd az adagolóba juttatja. Az adagoló ezt követően a különböző granulátumokat a recepturának megfelelő arányban a keverőbe adagolja, mely homogén granulátum keveréket képez belőle.
A felszívási folyamat lényege: a vákuumforrás által vákuum képződik a felszívó térben. A felszívó térből a granulátumhoz vezető csövön megindul a légáramlás, amely magával viszi a granulátumot. A felszívó tér belső kialakítása révén a levegőből leválasztjuk a granulátumot. A levegő pedig egy szűrőn keresztül a vákuumforrásként szolgáló oldalcsatornás vákuumszivattyúba jut, majd a légtérbe távozik.
A rendszer előnye, hogy a különböző granulátumokat nem kell előre többféle receptúra alapján összekeverni és tárolni, elegendő csupán az alapanyagok tárolását megoldani. Az aktuális igény szerinti keveréket az felszívó-adagoló-keverő egység folyamatosan állítja elő, így a szükséges receptúra váltásokat könnyen és gyorsan meg lehet valósítani, s a rengeteg receptúra kezelése egyszerű. (1. ábra)
Azok az üzemegységek, amelyek kevés receptúrával dolgoznak, nem mindig alkalmaznak ilyen felszívó-adagoló-keverő egységet, az alapanyagokat nem önállóan, hanem már adott receptúra szerint tárolják be a silókba. Mi is alkalmazunk ilyen rendszert az egyik telephelyünkön. Itt gépeinket túlnyomó részben silókból látjuk el különböző anyagkeverékekkel. A silókat légszállítással töltjük fel, de a granulátumot nem a vákuum szállítja, hanem az oldalcsatornás vákuumszivattyú nyomott oldalon kilépő nagysebességű és nyomású levegő. A vákuumszivattyú a levegőt egy levegőszűrőn keresztül szívja, így a granulátummal együtt csak tiszta levegő kerül be a silóba. Az extruderek kiszolgálása is a nyomott oldalon történik, a silókból egy légáramba adagoljuk a granulátumot, majd pedig egy ciklonnal leválasztjuk. (2. ábra)
A két rendszer alapvető különbsége a granulátum szállítás módja. Az alapanyagból felszívó-adagoló-keverő egységgel dolgozó rendszerben a granulátumot vákuummal szállítjuk, míg a keverékből dolgozó rendszernél nyomással szállítunk. Ha csak a szállítást nézzük, függetlenül, hogy előtte vagy utána keverjük össze a granulátumokat, akkor azt mondhatjuk, hogy a két módszer kompatibilis egymással. Azonban felfedeztük egy komoly hátrányát a piacon kapható felszívó-adagoló-keverő rendszereknek, mely éppen a szállítás módjára vezethető vissza.
Az extruder és a fej között helyezkedik el a szűrőváltó, és benne a szűrőbetét. A szűrőbetét feladata, hogy megfelelő ellenállást képezzen az anyagáramban, így az extruderben nagy nyomást hoz létre, ami szükséges az ömledék tökéletes homogenizálásához. Ezzel párhuzamosan kiszűri a granulátumból a különböző úton-módon belekerült legkülönfélébb szennyeződéseket. Azt feltételezzük, hogy a nagy nyomás és hőmérséklet hatására a szűrőn fennakadt szerves szennyeződésekben kémiai folyamatok mennek végbe melynek következtében ezek az anyagok bomlanak, kokszosodnak. A szűrő folyamatosan feltelik, eltömődik a szennyeződésektől, és így növekszik az ellenállása, ezért szükséges a szűrőbetét rendszeres időközönkénti cseréje. A szűrőcsere mindenképpen egy nagyon sarkalatos pontja a gép működésének, hiszen le kell hozzá állítani a gépet, ami jelentős időveszteséget, termeléskiesést okoz, valamint az újraindításkor selejttermeléssel jár, amíg újra beállnak az üzemi paraméterek.
Amikor egyik gépünket felszívó-adagoló-keverő egységgel láttuk el, a szűrőbetét a szokásosnál nagyobb mértékben, illetve rövidebb idő alatt szennyeződött el. Továbbá a rajta lévő szennyeződés a korábbiakhoz képest teljesen más jelleget mutatott. Így szükségessé vált a szűrőbetét gyakoribb cseréje, ami növelte az említett veszteségeket. A gyorsan és fokozottan jelentkező elszennyeződés, a gyakrabban szükségessé váló szűrőcsere, és az ahhoz szükséges gépleállítások, érzékenyen érintik a folyamatos gyártást, valamint a gyártás gazdaságosságát. Ezért fokozottan kezdtünk el foglalkozni a jelenséggel, felkutatni az okait és kidolgozni a lehetséges megoldásokat.
Az okok viszonylag könnyen feltárhatóak voltak a két rendszer tüzetes összehasonlításával. A legszembetűnőbb különbség a granulátum légszállításában mutatkozott. A hagyományos, silós esetben a vákuumszivattyú nyomott oldalával fújtuk a granulátumot, és a vákuumszivattyú egy levegőszűrőn keresztül szívta a levegőt, így csak szűrt, tiszta levegő jut a granulátummal együtt a silóba, illetve az extrúderbe. Míg az új, granulátum felszívó-adagoló-keverő egységgel ellátott rendszerben a vákuum szállítja a granulátumot, természetesen nagymennyiségű levegővel együtt. A vákuumszivattyú ebben az esetben is egy szűrőn keresztül szívja meg az adagoló feltöltendő terét, de a levegő, a granulátummal együtt a napi tárolóból érkezik és ez gyakorlatilag az adott légtér szűretlen levegője, mivel a szűrés csak a vákuumszivattyú szívócsonkjánál történik, és csak a szivattyúba kerülő levegőt szűri. A felszívó-adagoló-keverő egységgel ellátott rendszerben tehát a nagymennyiségű levegővel nagyon sok por, pollen és minden egyéb, a levegőben lebegő szennyeződés kerül a granulátummal együtt az extruderbe, hiszen a vákuum a terem levegőjével együtt szívja a granulátumot. A szennyeződések nagyon sokfélék lehetnek: a légkörben állandóan jelen lévő szennyeződések, por, korom és egyéb szilárd égéstermékek a közlekedésből és fűtési szezonban a tüzelésből, valamint tél kivételével virágpor és pollen egész évben. Ezek a szennyeződések okozzák a szűrő gyorsabb és jelentősebb elszennyeződését.
A szennyeződések bejutását jelentős mértékben fokozza, hogy a granulátum szemcsék a szállítás során folyamatosan súrlódnak egymáson és a csővezeték falán, ezáltal statikusan feltöltődnek, így fokozottan vonzzák a szennyeződéseket, amelyek a felületükre tapadnak. A tárolóedényből szívjuk ki a levegőt, melynek helyére folyamatosan friss érkezik, ami szintén tele van szennyeződésekkel, melyet a feltöltődött granulátum szemcsék magukhoz vonzanak és „beszállítanak” az extruderbe.
A szennyeződések mindig jelen vannak, csak az egyik esetben bejutnak a rendszerbe, a másik esetben pedig nem, pontosabban lényegesen kevesebb, hiszen előbb vagy utóbb minden esetben szükségessé válik a szűrőbetét cseréje. Persze mondhatnánk, hogy megfelelő üzemi körülmények, üzemi levegőszűrés és légkondicionálás segítségével ezek a problémák elkerülhetők lehetnének. Ezen megoldások műszaki kivitelezhetőségének nehézségei és jelentős anyagi vonzatainak felsorakoztatása helyett gondoljunk csak arra, hogy nagyon sok ember szenved ezektől az allergiát okozó szennyeződésektől. Az emberek védelme érdekében mindig jelentősebb erőfeszítéseket tesznek, de ezen a területen nem sikerült átütő sikert elérni, ez nem lehet véletlen. A megoldás nagyon nehéz és ha még emberi léptékben, emberek érdekében sem sikerült ez a problémát kiküszöbölni, akkor el lehet képzelni, hogy ipari méretekben milyen komoly nehézségeket okozhat egy tökéletes megoldás kimunkálása. Nem véletlenül említettük a levegőben lévő szennyeződések allergiát okozó részét, a pollent és társait, hiszen ezek kiszűrése a legnehezebb. Az év különböző szakaiban különböző mértékben vannak jelen, ugyanúgy az üzemekben, mint az emberek életében. Itt jutunk vissza cikkünk címéhez, a pollen allergiás extruderhez, hiszen ezen szennyeződés kiszűrése a legnehezebb, majdhogynem lehetetlen. Így más megoldás szükséges, mint pusztán a levegő szűrése.
A másik dolog, ami nem szerencsés, hogy a beszívott friss levegővel folyamatosan kerül be a rendszerbe a levegőben lévő vízpára. A vízpára részben szintén a granulátum felületére tapad, részben pedig a polietilén magába szívja a vizet, és így kerül be az extrúderbe. Az extrúderben lévő nagy nyomás miatt, a nagy hőmérséklet ellenére, a víz nem párolog el, hanem az ömledékkel együtt a fejbe jut, majd a szerszám résen kilépve számos problémát okoz a fóliában, illetve a ballonképzésben.
A rendszereket összehasonlítva, és a jelenségeket elemezve megállapíthatjuk, hogy a problémát a rendszerbe folyamatosan beáramló friss, szennyezett, párás levegő okozza.
Végezetül nézzük kicsit messzebbről és általánosabban a problémát, ezalatt azt értjük, hogy ne szűkítsük le vizsgálódásunkat csupán a közvetlen anyagellátásra. Kövessük végig a granulátum majd teljes útját, és induljunk el már az azt szállító tartálykocsitól. (3. ábra)
Az ábrán jól látható, hogy a bemutatott jelenség, mint szennyező veszélyforrás, azaz a friss, környezeti levegő bejutása a rendszerbe több helyen is lehetséges, és meg is történik. Ezzel csak azt szeretnénk érzékeltetni, hogy a probléma valóban hatékony megoldása csak rendszerben gondolkodva lehetséges. De induljunk el az anyagellátástól, mint a rendszer egyik legkönnyebben kézben tartható részétől, és a megoldásokat fokozatosan terjesszük ki az egész folyamatra.
Az anyagellátási rendszerre visszatérve a megoldás kézenfekvőnek tűnik, de mégsem olyan egyszerű. Hiszen ha jobban belegondolunk az egyik rendszer a másik fordítottja, mármint áramlástani szempontból. Az egyiknél a vákuumszivattyú nyomott-, a másiknál a szívott oldalával szállítunk. A levegőszűrő mindkét esetben ugyanott helyezkedik el, ennek ellenére az egyik rendszernél belekerül a szennyeződés a rendszerbe, addig a másiknál nem.
Szerintünk számos megoldás létezik, ennek fő oka a rendszerek különbözőségében rejlik. Mindenki egy kicsit másképp építi ki az anyagszállítási rendszerét a helyi sajátosságoknak, a gépek elhelyezkedésének illetve anyagigényének, valamint az alkalmazott keverési és ellátási rendszernek megfelelően. (4. ábra)
A mi rendszerünk esetében a granulátum kezelő egység felszívó körének zárt rendszerré történő átalakítása vált be leginkább. A kivitelezése is viszonylag egyszerűen megoldható pár csővezeték kiépítésével. A megoldás lényege, hogy a vákuumszivattyú nyomott oldalán légtérbe távozó szűrt, tiszta levegőt visszavezettük a granulátum tárolóban lévő felszívó csőhöz. A granulátum szállítására használt levegő így folyamatosan tisztán tartható, s nem kerül szennyeződés a rendszerbe.
A szivattyú nyomó csonkját szétágaztatva visszavezetjük mindegyik komponens szívócsövéhez. Felszíváskor mindig azon az úton megy a levegő amelyik komponenst épp szállítjuk. Ezt segíti elő az is, hogy a csövek nyílt vége a granulátum tároló alján helyezkedik el, így a felette lévő granulátum mint egy dugó funkcionál, s minimalizálja a rendszer tiszta levegő veszteségét, leredukálva az esetleges szennyezőanyag bejutásának lehetőségét. Az átalakítással, illetve a visszavezető csővezetékek kiépítésével a szűrők cseréjének ciklusa és a szennyeződés jellege is visszaállt a korábbi szintre. Emellett a felszívó rendszer hatékonysága is jelentősen megnőtt. Azonos idő alatt 20-25%-kal több granulátum szívható fel a tároló edényekből.
Tekintsék meg egyéb képeinket a témával kapcsolatban.
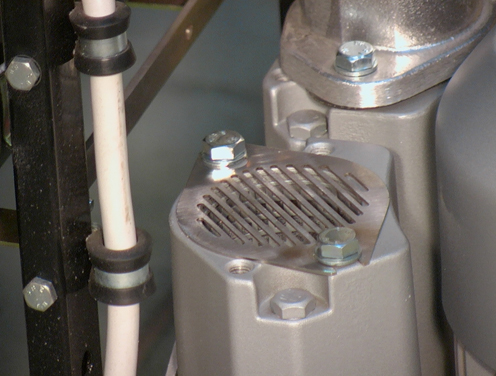
Fel